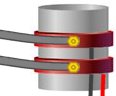
|
Home made sliprings. |
Page 1 | 2 |
Back to part 1
Next we'll look at the brushes.
If you can find them, carbon brush assemblies are the best option. It depends on the size and how easy they are to use. The brushes shown below are a good example, they are designed to handle several amps and are easy to mount.
This motor is is a series wound motor from a washing machine, but most washing machine motors are induction motors and don't have brushes, so check before ripping out the wrong type of motor. Also worth looking at are vacuum cleaner motors and cloths dryer motors. Vacuum cleaner motors are usually thrown away when the bearings get noisy, so ask your local electrical repairer to keep a few for you. Smaller motors, like hand power tools, have smaller brushes that are not easy to use, so give them a miss. |
|
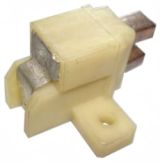 |
Vehicle alternator brushes are good,
you get two mounted in one package.
Starter motor brushes are better,
they will handle many tens of amps,
but can be fiddly to mount. |
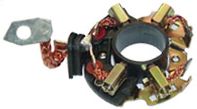 |
In keeping with the hardware store friendly design, I've chosen to use brass bolts for my brush material, brass is naturally slippery over steel and a reasonable conductor of electricity. If you have ever removed a vehicles steering wheel, you would have noticed the horn slip ring and brush. The slip ring is usually steel, and the brush is made from brass, so these are proven materials.
Try to find brass bolts with the widest head you can, and watch out for "brass coated" bolts, these will quickly wear. You could also use brass knobs for drawers, but these can get expensive.
Each slip ring will have two brushes, one on each side, to ensure a good contact with the slip ring. The brushes need to be sprung, so they are always pushing against the slip ring.
A common "springy" material we can use is steel strapping. This stuff is used to wrap up heavy loads, chances are the hardware store uses it to wrap up timber, ask the store man if they have some scrap strapping steel and I'm sure they will help. Cut the strapping into lengths and bend up as shown below. Double or triple up the straps for more tension.
Fencing wire is also very springy, and could be used as a substitute, however flat strapping steel has the advantage of keeping the brass bolts square against the slip rings, and less inclined to wander up or down
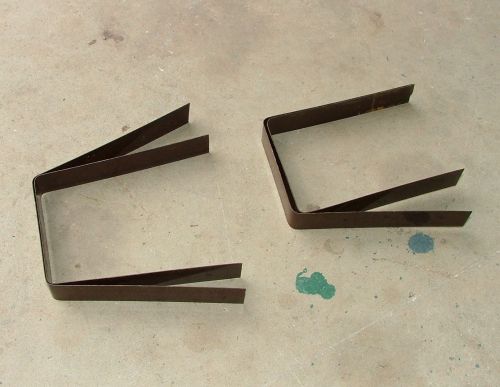
|
Next we need to make our brush holder. I used a length of 20mm square hardwood, and cut two recesses to keep the strapping square. The two holes are for the mounting bolts. |
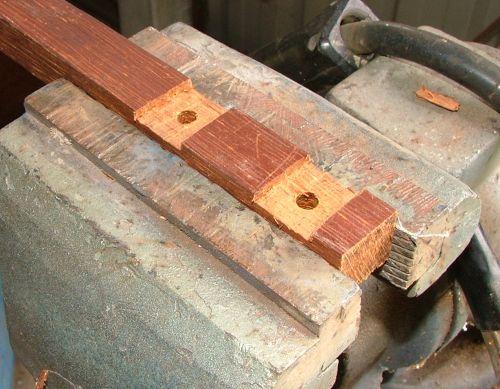 |
A trial assembly.
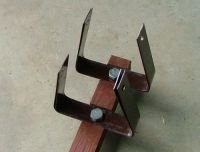
Check the brushes are on opposite sides of the slip ring, and the brushes don't foul the slip ring bolts. |
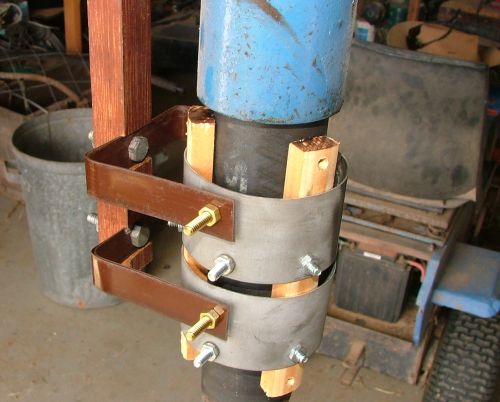 |
All wired up.
Power is fed to each brass bolt, don't rely on the steel strapping to feed power, as its spring tension will change if it gets hot.
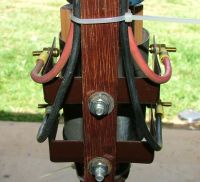
|
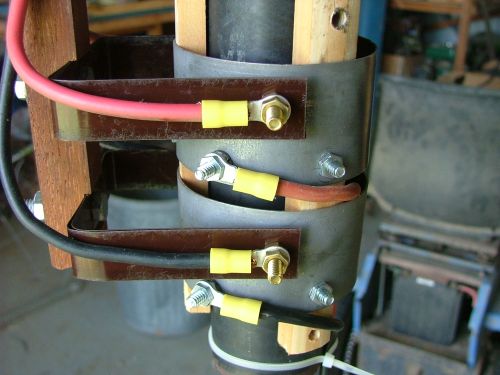 |
Another way to make brushes, not pretty, but works just as well.
2 hinges per slip ring. The hinges are offset to get them close together without touching. When you screw the hinges to the timber insulator, be careful the screws don't make contact in side the timber.
|
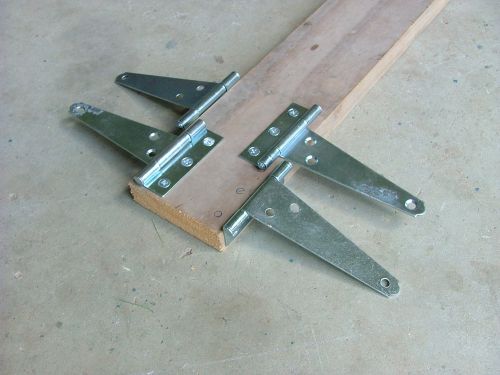 |
Trial assembly.
Again you need to adjust the brush assembly so the brushes are on opposite sides of the slip rings, and will not foul the slip ring bolts. |
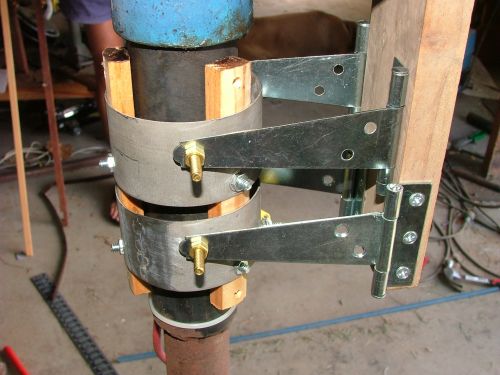 |
Springs are used to give the brush tension against the slip rings. You want a fair bit of pressure, but not too much to bend the hinges or scratch the slip rings. |
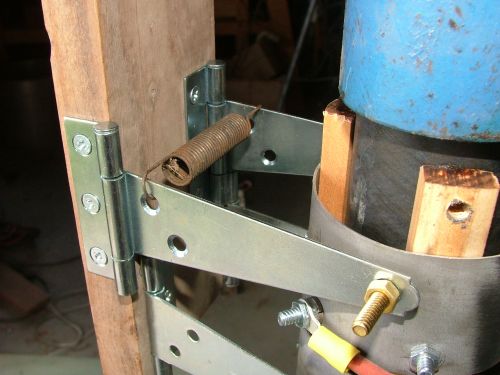 |
All wired up.
Once your slip rings and brushes are finished, you should cover them to keep out the rain. Moisture is the enemy of any slip ring, so keep them dry.
Bedding in the brushes.
To give a better electrical connection between the sliprings and brushes, wrap a layer of 100 grip sand paper around the slip ring, rough side out, and rotate the brush assembly around the slip ring for several turns.
|
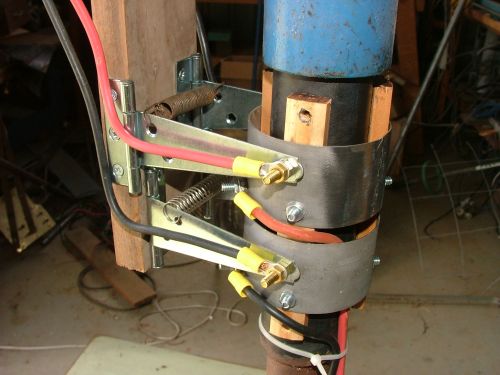 |
|