How to improve those cheap Chinese blades |
Page 1 | 2 | 3 |
Back to Part 2
The following is a summary of
other modifications made to these windmills by one of
our forum members.
In Kevin's words...
Dont know if many are interested,
but after the good advise on quieting the Chinese wind
mill I thought Id forward the improvements my
brother and I have done to our 2, 200w 24V mills supplied
by Jaycar, $450 each.
A bit of history.
We bought our first mill 13 months ago, and set it up
50m from the shed on its own tower. Not the best of
positions but this was the amount of cable we had at
the time.
Did not pay too much attention to assembly but every
thing went together OK.
First day, either we blew up the controller
OR it did not work out of the box.
So into the junk heap, find an old 12V 55amp car alternator,
this was stripped down to extract the rectifier 40 minutes
later, the old rectifier has a new life with mill ONE.
Old alternators are cheap, available
in the bush and easy to check just do a diode
check in each direction on each diode to see if they
only pass in one direction.
Dont have them connected to power when you do
this.
We dont have a dump load on our
mills, since our battery bank is so big the maximum
input of mill ONE of 10 to 12 amps is only a trickle
feed. Its an effort to get the batteries to float.
Battery bank - 2 old fork truck batteries 36 V 800 Ah,
cut and spliced to form 2 24V banks. These battery packs
were dead when we got them for $50 each six years ago.
Find and jump out the dead cells (usually only 1 or
2 cells) instant deep cycle BIG battery bank.
Power monitoring is performed via a
PL20 regulator using an external shunt resistor
Last year for October to December mill ONE averaged
20 Ah per day.
1 month ago we bought another wind mill.
Built a new 15m tower from old steel light poles.
Hopping for considerably better results we moved 60m
further up the hill.
(Got hold of more second hand industrial orange 4 core
cable)
We took more time with the assembly
this time, found the blade mount holes were way out
of align, quite a bit of filing to get the blades to
sit flush to the hub and properly spaced. At this point
we super glued 1.5 dia wiper snipper cord down the back
of the blade as suggested by the forum.
Rewired, the system for the 2 mills,
another car alternator (did not even take its own controller
out of the box)
Well apples arent oranges, same
goes for wind mills.
Mill TWO on its lovely new high tower was spinning faster
than mill ONE, good.
NO, yes mill TWO was spinning faster but was not making
any power?
(Mill TWO is considerably quieter than mill ONE even
going faster).
Mill TWO produces more power in high
winds than Mill ONE however the old mill starts producing
earlier and is better in light winds. We suspect that
one is in delta and the other is in star.
This is becoming a book, not a quick
note to the forum. Things can be expanded later if people
want to read the ranting of a mad power generator.
THE MODIFICATION
We observed that mill ONE tended to hunt around with
the wind, to be expected at only 4.5m above ground and
so low on the hill.
But it also seemed to start furling early and not maintain
output in strong winds.
The basic geometry of the tail is wrong,
in moderate winds the thrust on the blades allow the
mill to turn slightly away from the wind (as if starting
to furl)
The tail is not holding the mill into
the wind.
Now reading the guru of small wind turbines, Hugh Piggott
he suggests the tail should have a positive offset so
that under moderate winds the mill is held into the
wind slightly to the opposite side of furling.
Mod 1. - Bend the tail arm 10
degrees away from the axis of the wind mill.
While mill ONE was down we checked the
geometry.
The rack angle on the tail pivot is only 3 degrees,
too small to allow the tail weight to control the furling
of the mill.
Mod 2. Added %50 more
weight to the tail. Changed metal tail for a piece of
ply wood twice the area and heavier. (at present we
are only 0.5 kg heavier than the original vane but could
do with more weight)
RESULTS, mill ONE is more stable in
moderate winds and is holding a higher output in gusty
winds during furling operations.
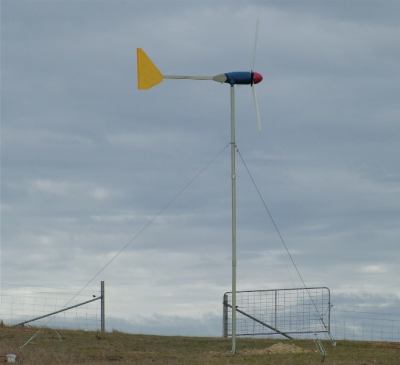
Picture of mill ONE, before tail mods.
Checking the tail angle.
Hold the tail arm against the stop on the housing and
sight along the axis of the generator. The tail should
move away from the axis by approximately 10 degrees
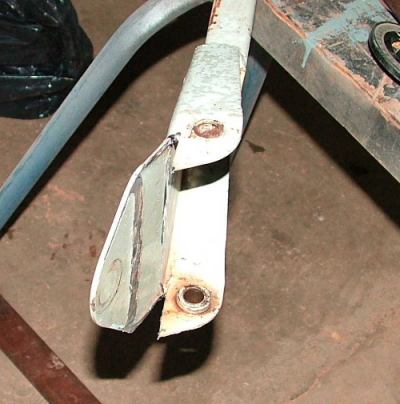
You can see how Dave (my
brother) cut the tail arm to get the added 10 degrees.
Just weld a filler in the slot and a splash of paint
if you are so inclined.
The tail size
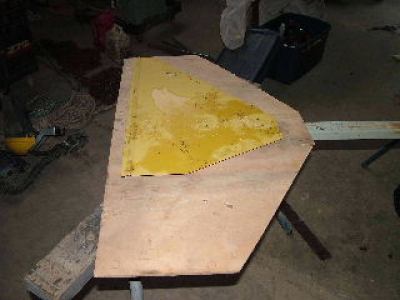
The tail was cut from some
scrap ply in the shed. I think it was 7mm thick
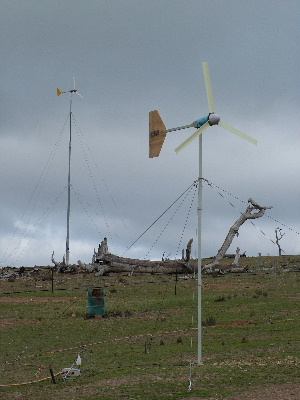
Pic of the 2 mills, mill
ONE is in the fore ground.
You might consider changing the bearings on the mill
before you put it up, we have just changed mill ONE,
after 18 months it developed a growl.
Thanks to Kevin (
KTee )
|