|
Page 3 of 3 |
Author |
Message |
dazz Regular Member
 Joined: 15/04/2008 Location: Posts: 78 |
Posted: 06:39pm 28 Jun 2008 |
Copy link to clipboard |
 Print this post |
|
Has anybody tried reducing the rapid power ripple associated with gust behaviour by employing a small flywheel on the turbine shaft?
If rapid gust peak energy could be storred as inertia and then released at a more gentle pace then it might be easier to track shaft power levels.
Just an idle thought :) But just thought I'd share in case it had some validity.
Daryl |
|
GWatPE
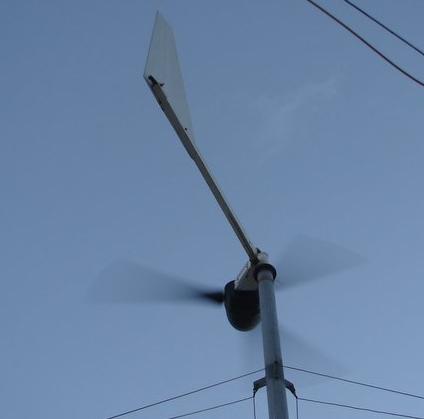 Senior Member
 Joined: 01/09/2006 Location: AustraliaPosts: 2127 |
Posted: 10:28pm 28 Jun 2008 |
Copy link to clipboard |
 Print this post |
|
Hi Dazz,
the effect of trying to store energy at the point of collection is essentially adding delay to the system rersponse to a wind gust. This is used in steady state processes to smooth a variable.
the effect is that the blade will be overloaded or underloaded for the wind energy in the gust at that moment. The blade has to be at the correct loading to extract maximum energy.
If a windmill generator is heavily overdriven, then MPPT is possibly no benefit. I think the MPPT should only refer to the wind energy, up to the point of mechanical, or electrical limiting systems. .. .. Gordon.
PS.
Hi Gill,
do you have any time line for a working design?
become more energy aware |
|
Gill
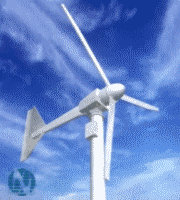 Senior Member
 Joined: 11/11/2006 Location: AustraliaPosts: 669 |
Posted: 03:35am 29 Jun 2008 |
Copy link to clipboard |
 Print this post |
|
Gordon,
I've got other projects on the go at the moment and will need to research buck converters a lot more before I'm able to build a prototype for myself. But I've put the concept out there that anyone can run with it if they like. With your expertise and existing boost/buck module you'd almost be there? Why not give it a burl?I'm working on it but am a bit of a plodder. Still I get there in the end. was working fine... til the smoke got out.
Cheers Gill _Cairns, FNQ |
|
dazz Regular Member
 Joined: 15/04/2008 Location: Posts: 78 |
Posted: 05:24am 29 Jun 2008 |
Copy link to clipboard |
 Print this post |
|
Thanks Gordon,
I thought there would be a problem with it, just couldn't see it before :)
What you say does make me wonder though. If a major problem with MPPT design for windmills is missing rapid wind transients then pre-conditioning the input energy to the shaft by use of something like a flywheel, might make missing such transients less problematic.
I think I understand what you are saying about where in the energy process conveyor belt that the MPPT should be concerning itself but perhaps a smart turbine design that lends itself to later incorporating an MPPT is not a bad way to go.
In designing a windmill there are already some designs that will work better with an MPPT than others. ie designs that perhaps have larger inherrent inertias like twin stator designs and windmills with 6 blades that present a higher torque to speed ratio response to the shaft and hence already are not so prone to very rapid speed changes in gusts. In these types of designs there already is added "flywheel" type energy storage and obviously could be still well designed not to have significant underloading or overloading problems associated with their extra inertia.
Anyway, this just goes back to a lot of what has already been discussed so don't worry to reply. It was just an afterthought.
Cheers, Daryl |
|
GWatPE
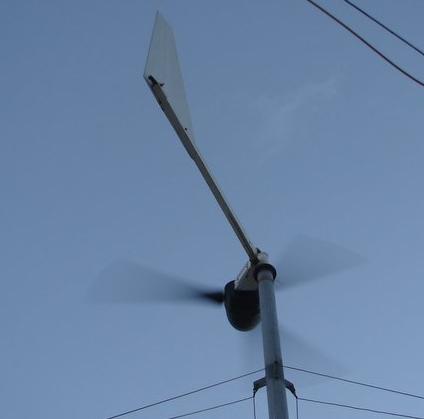 Senior Member
 Joined: 01/09/2006 Location: AustraliaPosts: 2127 |
Posted: 11:50am 29 Jun 2008 |
Copy link to clipboard |
 Print this post |
|
Hi Gill,
I can get time to look at this after I get back from my trip to QLD.
Hi other readers,
We have had good winds since last night. I have finished the 4 channel 100Hz logging module and I gathered an hours data at 5 sets of readings/sec. I was able to compare the power extracted from the wind and the power delivered to the battery with the wind energy.
these are the efficiencies at various wind energy power levels.
at 5W >>> 60%
10W >>> 73%
20W >>> 86%
40W >>> 93%
80W >>> 96%
160W >>> 97%
240W >>> 97%
The unit is not perfect, but this represents a windspeed range of about 2m/s to 9m/s. The power maximizing performs better at the high power levels, which helps keep components cool. Most of the losses seem to be inductor related as the mosfet and steering diodes temperature only rose 4degC at the peak power levels. At the bottom end of the power spectrum, the inductor flyback voltage has to provide a gain of almost 5, to enable battery charging. I consider that to lose 1/3 of the power at the 5W level is OK. Anything is better than 0 at this low windspeed.
I have to add the shutdown componentry for battery protection, and that is about it.
I have to batten down the hatches as we are supposed to be in for a gale tonight and tomorrow. All good for RE windmills.
Cheers, Gordon. become more energy aware |
|
Gill
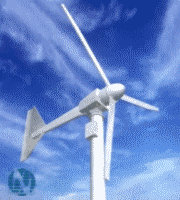 Senior Member
 Joined: 11/11/2006 Location: AustraliaPosts: 669 |
Posted: 01:03pm 04 Jul 2008 |
Copy link to clipboard |
 Print this post |
|
Earlier in this thread I commented PWM could be made to track fast rise and falls by increasing the increment size. The down side of this is that the finer adjustment is lost.
This code below takes the difference in the monitored value and uses that to set the duty. Hence: small change = small increment, big change = big increment.
even larger increments can be set by multiplying this difference by another number. In the example, I have multiplied the difference by itself but a cube or other power is possible too.
#REM Dom's Wind Power Tracker
Version 1.2 4th July 2008
#ENDREM
#picaxe 08m
symbol duty = w0
symbol oldamps = b2
symbol newamps = b3
symbol difference = b4
Setup:
duty = 500
Run:
readadc 1, newamps ; read in amps
if newamps > oldamps then
if duty < 1000 then
difference = newamps - oldamps
duty = difference * difference + duty max 1000 ; up duty if more
endif
else if duty > 500 then
difference = oldamps - newamps
difference = difference * difference
duty = duty - difference min 500 ; down duty if less
endif
pwmout 2, 249, duty ; adjust pulse width
oldamps = newamps ; reset
goto Run
END
Yes, there is a couple more lines of code to run but this slows only the finest adjustment of 1, where as when fast adjustment is needed this eats it up super fast. Edited by Gill 2008-07-05 was working fine... til the smoke got out.
Cheers Gill _Cairns, FNQ |
|
GWatPE
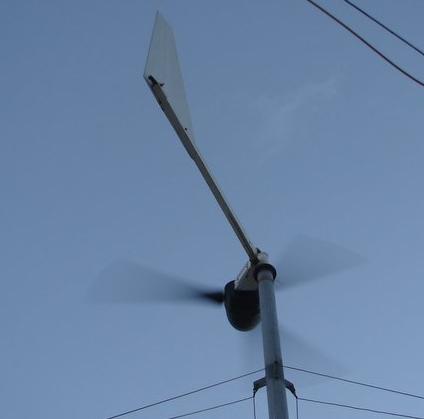 Senior Member
 Joined: 01/09/2006 Location: AustraliaPosts: 2127 |
Posted: 03:07pm 04 Jul 2008 |
Copy link to clipboard |
 Print this post |
|
Hi Gill,
More gain in the control loop can lead to runaway oscillations, and eventually to ON/OFF control. This will then require dampening, that will defeat exactly what you are trying to achieve. .. .. Gordon. become more energy aware |
|
Gill
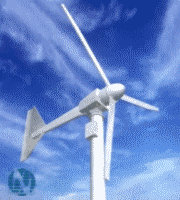 Senior Member
 Joined: 11/11/2006 Location: AustraliaPosts: 669 |
Posted: 03:35am 05 Jul 2008 |
Copy link to clipboard |
 Print this post |
|
Gordon,
Quite so. As I have said, we need to select the correct increment.
At least now we have a choice of up to supa turbo corrections where needed with fine correction in the one package.
Your warning is appreciated and I feel most applies as the PWM frequency gets higher and the max duty range decreases significantly then over compensation becomes more likely. was working fine... til the smoke got out.
Cheers Gill _Cairns, FNQ |
|
domwild Guru
 Joined: 16/12/2005 Location: AustraliaPosts: 873 |
Posted: 12:08pm 12 Sep 2008 |
Copy link to clipboard |
 Print this post |
|
Thanks for all the answers and suggestions. "Brainstorming" can always lead to correct solutions.
Taxation as a means of achieving prosperity is like a man standing inside a bucket trying to lift himself up.
Winston Churchill |
|
|
Page 3 of 3 |