Author |
Message |
drewgarth
 Newbie
 Joined: 30/07/2006 Location: AustraliaPosts: 8 |
Posted: 02:48pm 19 Sep 2012 |
Copy link to clipboard |
 Print this post |
|
Hi Folks,
Im having trouble soldering the ACS758.
(Glenn thanks for your article on the site its really useful).
Having made a PCB, with 2Oz copper on both sides and drilled the hole pattern to match the Allegro specs, im struggling to get the solder to stick to the ACS 758.
Not surprisingly my small electronics iron, had no chance so i switched to a gas iron with a heavy tip and slowly increased the heat.
The problem im getting is that the solder readily pools on the copper PCB surface but wont stick to the ACS758. That is, until i really heat it up.
I seem to have cooked the ship, because at zero current its output is not half of the supply voltage.
This is my first experience with relatively heavy gauge electronic components.
Do I need to clean/sand the pins on the chip?
Perhaps i need the soldering iron hotter, so I can apply the heat for a shorter period.
Am I better to heat the pin on the chip with the soldering iron as I melt the solder, or let the molten solder transfer heat to the pins.
Im hoping that someone can give me a few tips because trial and error with these chips will get expensive ...
Thanks in advance for any advice
cheers
Andrew |
|
Downwind
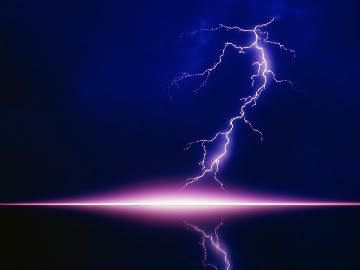 Guru
 Joined: 09/09/2009 Location: AustraliaPosts: 2333 |
Posted: 07:54am 20 Sep 2012 |
Copy link to clipboard |
 Print this post |
|
What is the full part number for the allegro chip you have?
There is 2 types of chips a Unidirectional, and a Bidirectional chip, the Unidirectional chips start close to zero volts out with zero amps and go full scale to 5v out at the full amp rating, where the Bidirectional start at half rail voltage and increase or decrease the V-out depending on the direction of current flow.
So you may or may not have damaged the chip depending on which chip you actually have.
To solder them you need a good hot iron and apply the heat to the heavy leads and keep adding a dob of solder till it flows onto the leg then flow the solder onto the board, you will have trouble if you try to solder the leg to both sides of the board as the leg being the heaviest conductor of heat here will desolder the opersite side while you try to solder the other side.
This is why i suggested to Glenn to use a strip of copper sheet and make a tag that the leg passes through and the bolt goes through the copper tag + pcb, and solder the tag to the leg, using the PCB to support the tag and bolt and chip.
They will handle quite a bit of heat and need to with such heavy copper legs to solder onto, the thing to try to avoid is slow long prolonged heating, as this will just tend to bake the chip over time and still not solder it in place.
Pete.
Sometimes it just works |
|
drewgarth
 Newbie
 Joined: 30/07/2006 Location: AustraliaPosts: 8 |
Posted: 10:21am 20 Sep 2012 |
Copy link to clipboard |
 Print this post |
|
Thanks Pete,
some good advice!.
Firstly the chip is the bi-directional version. The 50amp and also on a separate board the 200amp version.
Using a supply voltage of 5.05v
With the 50amp chip I get 2.59 out which is incorrect
With the 200amp chip i get 2.52 out which is correct.
Interestingly the 50amp chip still appears to function. I drew 2amps through it and the output varied appropriately. Just incorrectly offset.
Your advice of what not to do is exactly what i did do. I was trying to avoid heating the leg too much, so I think that i slowly cooked it.
The 200amp version I did slightly differently, when the solder pooled on the PCB and not to the leg, I tried brute force and used the gas flame on the gas iron directly for a few seconds. That worked (on both sides), but I was worried the fact it worked may have just been luck rather than a repeatable practice.
I have some more of the chips on their way, so I will try again since I have another PCB made up and then try the copper tag idea. |
|
Downwind
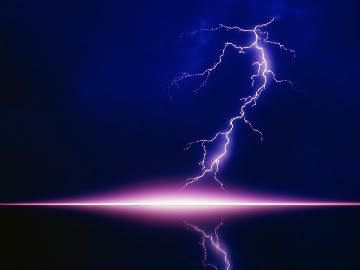 Guru
 Joined: 09/09/2009 Location: AustraliaPosts: 2333 |
Posted: 05:19pm 20 Sep 2012 |
Copy link to clipboard |
 Print this post |
|
Depending on your application and if you need to read the current both ways, but i like the Unidirectioal chip much better, as the resolution of the readings are far greater because you have the full 5v range for the full amp range and not just from half rail.
The output at zero amps can vary slightly due to the temperature of the chip, so if you tested it after soldering it might have been effected by the temp.
200 amp through the copper on PCB might be stretching the friendship a little and is why i use the tag method.
A bit of copper pipe split and flattened out will make good tags if you have no copper sheet, just cut a small chunk of steel to the square pin/leg size, and use that to punch a square hole in the copper sheet on a block of wood, to neatly fit the chip leg, a neat fitting hole will solder easier and be stronger.
I see no problem with the gas flame method if a little care is taken, sometime i do it in reverse and use the flame to preheat the leg quickly and then use the soldering iron to do the final solder joint, once the leg is up to temp the iron will normally work well.
Do what works for you, but either way the leg will need to get to around 300C before the solder will flow onto it, in most cases chips have a 300C solder rating for X seconds.
Pete. Sometimes it just works |
|
drewgarth
 Newbie
 Joined: 30/07/2006 Location: AustraliaPosts: 8 |
Posted: 06:57pm 20 Sep 2012 |
Copy link to clipboard |
 Print this post |
|
Thanks Pete very useful.
The reason for the double sided PCB, is that I was following Allegro's reference development board. Which to be honest is one of the most simple ways to get up and running with the chip. I have been using this for a year or so now regularly drawing 120+ amps without problem to date. Though i was very sceptical at first.
I tested the chip again this morning with the same voltage readings. Just to be sure it wasn't a residual temperature effect.
The only reason for changing from the development PCB is that I am trying to tidy things up a bit and include a few other items on the PCB, Voltage Sense, Rain tank pressure sense and feed it all the to the Arduino housed in a nice neat box. Hence I was trying to get it all on one PCB that sits nicely on top of the Arduino.
Having said that, the copper sheet/pipe idea is very rapidly becoming my preferred solution for the high current side of the circuit. It also gives me a far more robust option for attaching battery cables to.
Cheers
Andrew
|
|