Downwind
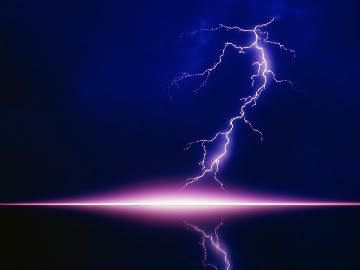 Guru
 Joined: 09/09/2009 Location: AustraliaPosts: 2333 |
Posted: 08:55pm 06 Sep 2013 |
Copy link to clipboard |
 Print this post |
|
As there has been a lack of posts on projects from our back sheds of late, here is one i bashed together a few months back, i was told it will never make the "Home and Garden " magazine for looks, but it has kept my butt warm last winter.
I had intended to hold off posting about untill i had some better photos, but like most things i havent got around to doing that.
THE UGLY DUCKLING!
Over time I have built several cylinder fire heaters, from recycled metal cylinders, like large LPG gas bottles (4 foot high ones) and the inner tanks from old mains pressure hot water heaters, both gas and electric HW Heaters, and other cylinders like 70L drums welded together, all have been for shack or shed heaters where looks were not important but good efficient heat was important.
Adelaide winters can be bloody cold at times and as I get older I find the need to warm the bones of my body and not just the surface skin area.
With reverse cycle air conditioning I find it only warms my outer body and not the inner core, and 30 minutes after turning the AC off im cold.
This year I decided to build and install a wood fire heater and its what this post is about.
As winter closed in it became a bit of a rush job to assemble a heater and installed it, or winter would be over and I suffer another year of a cold ass.
After a quick look around to what I could use for a cylinder, I decided 2 stainless steel beer kegs welded together would suit the requirements, and I just happened to have a few left over from the days I brewed my own beer.
Stainless is such a bugger to work with, I cursed myself several times during the build that I chose stainless, as its so hard to get good results if you don’t have all the right gear to work with SS.
I cut the tops off 2 kegs using a cut-off wheel on the angle grinder and beat one of the kegs out to overlap the other a little, and used the oxy torch to weld the 2 together, yes I have several other welders like stick and a mig but a roll of SS mig wire and the bottle of gas was way to costly for a small project, and about 2mm wall thickness was on the limit for arc welding with stick electrodes.
Tig would have been nice to have, but don’t have one and worked with what I have, besides fusion welding SS with a oxy is not so hard if you know how and the tricks of how to do it.
I learnt the tricks while welding the 1.2m circumference of the 2 kegs, practice makes perfection.
Then it was cutting 3 holes in the kegs for inlet air, exhaust flue and a door to add the wood through, the inlet and outlet was done on the back side, they really don’t matter where they are positioned other than at the bottom for air in and the top for exhaust gasses out, in my case I wanted a sealed fire and no risk of hot bits falling outside the cylinder, and on the flue side I wanted to be able to boil the kettle on top, this meant the flue needed to come out the back and not the top as I have always done in past builds.
The tube between flue and air inlet was a experimental thing to try to re-burn some of the emissions, and uses a venturi, but I can say that really works and is worth doing.
The door I cut too big in height as I worked between the two rolled ribs in the kegs, the problem with the height of the door allowed some smoke to be sucked out when the door was open to add wood, a internal plate was added temporary to restrict the door size, this solved the escaping smoke problem.
There is still several small things to fix and change but decided to do that next summer after winter is over, as the whole fire is designed to be removed in summer and stored in the shed, the inner flue just drops out of the ceiling and the sack trolley slides under the fire and I wheel the whole lot out to the shed.
The fire starts to emit heat almost instantly from the time its lite, and by the time the kindling wood has burnt down and larger wood is added, its time to start to throttle it back as the room is warm, within 30 minutes of lighting the fire the room temp has risen by about 6-7 degrees and an hour of full throttle fire increased the room temp from 14C to 30C, a little too hot and I needed to open the doors to other rooms, on average with a slow burning fire it warms the whole house over several hours, and consumes about a shoe box of reasonable quality wood a night.
Overall im very happy with how well it works, and the ugly duckling becomes a beautiful swan on a cold night.
To give an idea of the heat emitted, I noticed yesterday the paint on the architrave
Around a door 800mm away has started to blister, another job to fix for summer time now.
>>>>>>>>>>>>>
Years ago I worked for a small company that built in house fire places and learnt to understand how to best extract heat from a fire, although the company view was for looks first and efficiency second, my view is efficiency first and looks second.
If I can bore you with a few simple facts of extracting good heat from a small fire.
Most fires look good but preform poor, and we need to look at the basics to understand why.
A fire makes super heated gasses (smoke if you like) and it needs to go somewhere so it can breath and make more super heated gasses, now the average fire emits the gasses directly up the flue, but that is 90% of the heat wasted, where a cylinder fire stores the gasses or slows down the flow of gasses between the fire and flue to allow a better extraction of heat, with extracting the heat from the gasses it also shrinks the gasses some, making room for more gasses before it emits out the flue.
The other advantage with a cylinder is its mass surface area to the surrounding air, as metal can only conduct heat to air at a given rate, the higher the differential temp the slower it conducts to the surrounding air on a ratio of temp to air conductance, so to have a mass area of hot metal works far better than a small area of red hot metal as the thermal conductance of air is only as good as “X” regardless how hot the metal is.
Because the gasses are shrunk with cooling the need for a large flue diameter is reduced, along with only needing a small fire base to produce good heat, this also helps to control how fast the smoke exits the fire, in my case I use a 4 inch flue where most fires start with a 6 inch flue or larger, I don’t have a smoke problem (other than the door was too big) and the flue gets hot but not what I would call excessive in heat so that implies the balance of size and emissions is about correct.
I have a butterfly air control ( like the air control on a cars carbi) on the air inlet and a butterfly control on the flue outlet, the air in is the main adjustment to control the burn, although the flue control can make a big difference to the heat emitted, but the flue control can also make the fire leak smoke into the room, it’s a suck it and see operation to find the best operating position, and unless you are prepared to take the time and find the sweet spot to balance air in to exhaust gasses out, the flue butterfly is not really required.
I mainly use it for the end of night where the fire is no more than glowing coals with almost no smoke just heat, where I close the flue outlet down and extract as much residual heat from the remaining glowing coals.
Pete.
Sometimes it just works |
Downwind
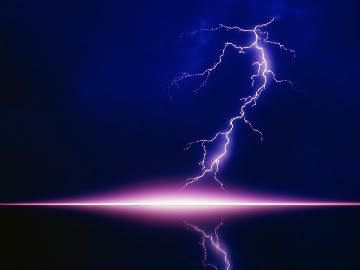 Guru
 Joined: 09/09/2009 Location: AustraliaPosts: 2333 |
Posted: 11:08pm 06 Sep 2013 |
Copy link to clipboard |
 Print this post |
|
Norcold,
Think of it as heating metal for fusion welding, if the air conducted at a equal rate to the metal temp, we would never get the metal hot enough to melt it together, what might be seen as thermal loss to the air.
Same with a fire, if the air conducted in a linear scale the metal would never get red hot, but there is a area of temp that you get maximum conductance to the air for the fuel burnt, so red hot is just burning excess fuel and venting lots of heat up the flue because the surrounding air can not conduct or sink the heat generated fast enough to balance the fuel consumed to produce the heat..... so wasted heat emissions.
More fuel = more heat, but there is a point you also get a lower heat return for the fuel used.
Pete. Sometimes it just works |
Downwind
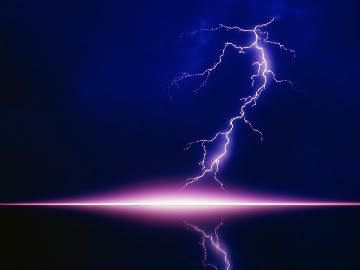 Guru
 Joined: 09/09/2009 Location: AustraliaPosts: 2333 |
Posted: 12:58am 07 Sep 2013 |
Copy link to clipboard |
 Print this post |
|
Bob,
No orders its my butt warmer and the rest of you can build your own if your arse is cold.
I did think of adding some copper coils to produce extra hot water, as by the time i want a late night coffee the fire is almost out and the kettle just warm. so to heat and store hot water would be an advantage.
It takes little energy to keep temperature in water, but a lot of energy to get it up to temp in the first place.
Although its less efficient i would add the copper coils to the outside, for the simple reason others see them and ask why the copper tube??
I have been told it looks like something from the swamps of Tennessee, so to add to the thought is all good with me.
Hey its only a project to post, i dont claim it to be the ducks nuts of heaters, althought it works well for me.
Pete. Sometimes it just works |