Author |
Message |
Grogster
 Admin Group
 Joined: 31/12/2012 Location: New ZealandPosts: 9306 |
Posted: 06:49am 05 Nov 2018 |
Copy link to clipboard |
 Print this post |
|
How the hell do METAL gaskets work?
The softer ones made from cardboard, gasket paper/card, or the manifold gaskets that are metal but with a compressible inner material I understand.
The all metal ones make me uneasy. Metal is not compressible when used as a gasket, so how the hell does it actually seal?
Take this metal gasket:

It is from a 1979 Vauxhall Chevette, but was also used in the Vauxhall Viva's, and the Holden Torana's(as they had the same engine).
I note the ridges around the holes. They squish down flat, as old ones taken off engines don't have those, they are just flat. That must be part of the thing.
This intake gasket makes me nervous, as the two big holes are the intake ports(which is fine), but the two medium sized holes in the middle are water-jacket holes for water from the cooling system to heat the intake manifold. How can metal seal against water? One would think that water would instantly leak from around those holes, and - God forbid - be sucked towards the intake ports. That would be REALLY bad, as trying to compress water in a cylinder will blow holes in things internally - not good.
I would love some mechanics on the forum to reassure me and explain to me how a metal gasket can possibly work as a seal where water is concerned. Edited by Grogster 2018-11-06 Smoke makes things work. When the smoke gets out, it stops! |
|
Revlac
 Guru
 Joined: 31/12/2016 Location: AustraliaPosts: 1024 |
Posted: 08:28am 05 Nov 2018 |
Copy link to clipboard |
 Print this post |
|
I know what you mean, they used to work most of the time, with good toque on the bolts. Just recently had head gasket issues with the Mitsubitchy Maggot, The steal rings would not compress enough around the cylinders (on the new Gasket) and let the water out of the water jacket. I suspect the metal rings were not to the standard quality.
Anyway If one is worried about it leaking, what we used to do with the old ford XY when replacing the head gasket or other manifold gasket, we get an old tin of silver/aluminum paint that has not been shaken or stirred for years, get the thick stuff from the bottom and paint the gasket with it, always worked, just did the same thing with the Magna.
Anyone else heard of this? Or do people just put this high temp silicon sealant on everything these days.
I haven't really answered your question Grogster. "How they work" As they often don't Edited by Revlac 2018-11-06 Cheers Aaron Off The Grid |
|
Grogster
 Admin Group
 Joined: 31/12/2012 Location: New ZealandPosts: 9306 |
Posted: 08:35pm 05 Nov 2018 |
Copy link to clipboard |
 Print this post |
|
Crafty idea on the paint-goo. Never heard of that one. I have also used that Automotive goo, which tends to be Gray in colour and you can use it on just about anything except head gaskets. I have mounted the carby back to the engine now, so can't use any goo ideas. Even the workshop manual just says: "Install a new metal gasket when you replace the intake manifold."
I did the bolts up reasonably tight, in a staggered pattern for even tightening.
[Quote=Revlac]I haven't really answered your question Grogster. "How they work" As they often don't [/Quote]
Well, that makes me feel much better.....
Thanks for your post. Still very interested in any other members views on this. Smoke makes things work. When the smoke gets out, it stops! |
|
M Del Senior Member
 Joined: 09/04/2012 Location: AustraliaPosts: 155 |
Posted: 06:58am 06 Nov 2018 |
Copy link to clipboard |
 Print this post |
|
Never used silicon on these things, there is a multitude of goops that will do the job.
On the exhaust side use maniseal, comes in a tube and seals well in exhaust heat. I think it very slightly expands to fill all voids and eventually sets like concrete.
On inlets with water jackets we used something like "rolls royce????" gasket goo/compound. It is blue, came in either a tube, spray can or tubs of varying sizes. Paint or spray it on, wait a moment for it to almost go tacky and then assemble. This one can be used on head gaskets. Never had a failure that wasn't broken bolts etc.
quick google before posting
http://hylomar.com/hylomar-product-range/gasket-jointing-compounds/
Developed in conjunction with rolls royce.
Current cost unknown, last bought it 1999/2000, sh*t, that long ago, damn I am getting old. Used it last year, still good.
Mark |
|
yahoo2
 Guru
 Joined: 05/04/2011 Location: AustraliaPosts: 1166 |
Posted: 03:00am 07 Nov 2018 |
Copy link to clipboard |
 Print this post |
|
the way it works is the two mated surfaces are perfectly flat and parallel machined. they will also be quite stiff like cast alloy parts.
So the gasket is only compressing and conforming .00625 - 0.1 of a mm and the stud/nut tension clamps it tight. Pliable gaskets are used on sheetmetal parts that can flex but they are poor at holding high pressure liquids or gases.
Also metal gaskets dont decay over time with extreme heat.
hylomar is a non setting compound for machines that need to be disassembled and inspected regularly and the gasket needs to be reused. normally the gaskets with crush rings are supposed to be installed dry and not reused. I'm confused, no wait... maybe I'm not... |
|
Grogster
 Admin Group
 Joined: 31/12/2012 Location: New ZealandPosts: 9306 |
Posted: 05:47am 07 Nov 2018 |
Copy link to clipboard |
 Print this post |
|
Useful info, thanks. 
I never reuse old gaskets, I always install new ones.
I don't understand how the crush-rings work. When squished, they will flatten out - fine. How does that help to seal? Smoke makes things work. When the smoke gets out, it stops! |
|
M Del Senior Member
 Joined: 09/04/2012 Location: AustraliaPosts: 155 |
Posted: 06:53am 16 Nov 2018 |
Copy link to clipboard |
 Print this post |
|
The crush-ring fills in any deformities in the mating surfaces and provides a seal against gas etc.
From memory, the material of the crush-ring in your picture is bulked up by the ring making process. ie, when in the press they punch the holes then press the rings, slightly enlarging the port hole and providing a small amount of crush material to make the seal. When bolted together the indented raised ring crushes, the inner port hole remains the same size. new gasket 2cm hole, used gasket 2cm hole, crush ring now flat.
Some also used an etched soft copper layer or similar addition to the indented ring to enhance the seal.
Hope this helps
Mark |
|
Grogster
 Admin Group
 Joined: 31/12/2012 Location: New ZealandPosts: 9306 |
Posted: 07:08am 16 Nov 2018 |
Copy link to clipboard |
 Print this post |
|
Very useful, yes, thanks.  Smoke makes things work. When the smoke gets out, it stops! |
|
Phil23 Guru
 Joined: 27/03/2016 Location: AustraliaPosts: 1664 |
Posted: 09:40pm 21 Dec 2018 |
Copy link to clipboard |
 Print this post |
|
Also don't believe everything you first read.
Recent experience the a 6 Cyl OHC Falcon head gasket; leaking HG's are not uncommon. (2000 model)...
So off it comes, gets machined & honed & ready to refit.
Torque Specs were 40nm + 90°, as per most website hits & the factory manual I have here.
Then start seeing a few suggestions of 30nm + 120°??? This is meant to solve future problems.
After seeing a few more hits on the different specs, I tried to track down a source; Turn out to be a Ford Technical Service Bulletin, issued a few years down the track.
So 30nm + 120° it got. Will see how it is down the track. |
|
isochronic Guru
 Joined: 21/01/2012 Location: AustraliaPosts: 689 |
Posted: 12:36am 23 Dec 2018 |
Copy link to clipboard |
 Print this post |
|
IIRC the metal gaskets had a "varnish" ie coating which created the seal, as it became pliable under heat and pressure. They were not reusable, and sometimes would not separate without a lot of grunt (and damaged cylinder heads). |
|
JohnS Guru
 Joined: 18/11/2011 Location: United KingdomPosts: 3800 |
Posted: 08:02am 04 Apr 2019 |
Copy link to clipboard |
 Print this post |
|
Maybe they do in fact crush (deform) but just the tiniest amount.
Where that amount is enough to fill in the gaps that otherwise would let gas (or liquid) out.
Another case is the copper washer (er, banjo?) used in brakes. You can only reuse them if you anneal them (I just buy another instead).
Most (all?) of the joints in metal brake lines (aka brake pipes) are metal-to-metal and seal against quite high pressures if done right.
John |
|
yahoo2
 Guru
 Joined: 05/04/2011 Location: AustraliaPosts: 1166 |
Posted: 05:51am 09 Apr 2019 |
Copy link to clipboard |
 Print this post |
|
I have repaired a lot of engines and after a while you pick up a few things.
A good quality metal gasket can be reused 5 or 6 times if it is doweled into position and goes back exactly in the same place. The modern gaskets on GM engines are particularly good. if you open it for inspection there is every chance it will go back together with the same metal gasket, if a new part is fitted it will need a new gasket.
it is normal for heads to bow slightly along their length, this will be pulled out by the head studs, its perfectly normal. Looking for defects in the head surface is done with a small steel straight edge ruler. You are looking for small areas around the cylinders and water jacket that are low. use a flashlight behind the ruler and look for light under the straight edge. there are gauges to measure flatness and decide if it needs machining.
High spots on the head and the block can be removed with a new knife sharpening stone ( the fine side) lube it with wd40 or similar product and keep checking with the tiny straight edge, it also gives some grain to the mating surfaces so they bite into the gasket. 90% of blocks and heads dont need fancy machining unless there is obvious damage. Pay particular attention to the area up against the dowels in the block. it is better to leave the dowels in and work around them if possible.
clean all surfaces and holes with compressed air and plenty of brake cleaner.
head bolts if you use an electronic tension wrench you can find out the tension of the head bolts before the engine is disassembled then these can also be used again. For a vehicle that is going to do 200,000+ after a rebuild it is not worth it just buy some new stuff but for engines that get regularly disassembled it is a waste of money replacing perfectly good bolts.
I'm confused, no wait... maybe I'm not... |
|
Warpspeed Guru
 Joined: 09/08/2007 Location: AustraliaPosts: 4406 |
Posted: 10:26pm 09 Apr 2019 |
Copy link to clipboard |
 Print this post |
|
I have successfully used high melting point front wheel bearing grease on most of my gaskets with great success. It all comes apart very easily, and the gaskets are reusable too, and its very easy to clean both the surfaces and the gasket, apply fresh grease and put it all back together.
Cheers, Tony. |
|
dwyer Guru
 Joined: 19/09/2005 Location: AustraliaPosts: 574 |
Posted: 07:35am 10 Apr 2019 |
Copy link to clipboard |
 Print this post |
|
Hi Tony what sort of car you did on gasket as my ford territory tubro has replace casket fews time as 2 or 3 bolts come loose mosty on number 6 cylinder exhaust thinking drill hole on bolt head and wire up like use aircraft piston engine sometime i get mad thinling about weld the bolt on the mainfold but not yet |
|
Warpspeed Guru
 Joined: 09/08/2007 Location: AustraliaPosts: 4406 |
Posted: 08:09am 10 Apr 2019 |
Copy link to clipboard |
 Print this post |
|
Drilling high tensile bolt heads for safety wire is not going to be that easy, but if you can do it, its an excellent solution.
Something a bit easier might be home brewing some bolt locking tabs from thick gauge sheetmetal.
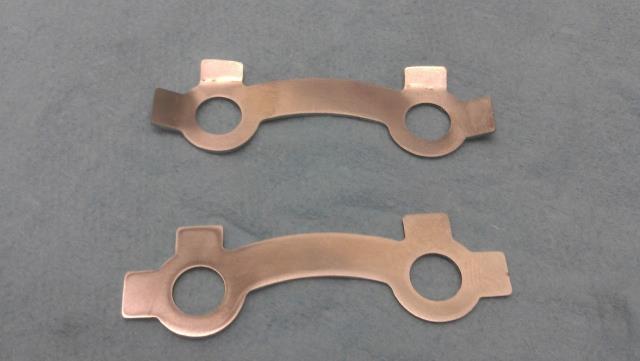
I only use grease on gaskets that have to seal against air or water. Cheers, Tony. |
|